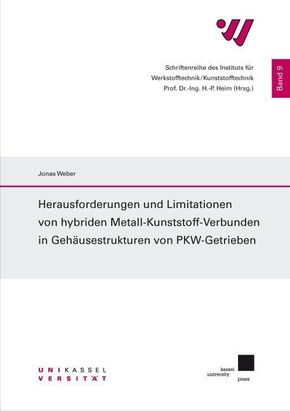
Herausforderungen und Limitationen von hybriden Metall-Kunststoff-Verbunden in Gehäusestrukturen von PKW-Getrieben
Verlag | kassel university press |
Auflage | 2019 |
Seiten | 153 |
Format | 21 cm |
Gewicht | 230 g |
Reihe | Schriftenreihe des Instituts für Werkstofftechnik / Kunststofftechnik 9 |
ISBN-10 | 3737606749 |
ISBN-13 | 9783737606745 |
Bestell-Nr | 73760674A |
https://www.upress.uni-kassel.de/katalog/abstract.php?978-3-7376-0674-5
The use of plastic-metal hybrid components in transmission housings opens up a new possibility for lightweight construction. Closed housing structures made of a single material can be replaced by open, load-optimized housing structures that offer an otherwise unattainable weight advantage through the use of plastics.The investigation of the bond strength between metal and plastic is an essential part of this work. The adhesion promoters investigated make it clear that there are currently no systems known to the author that can improve the bond strength of not only freshly molded components in the long term.The shot peening process already used for a large number of transmission housing types also opens up advantages for plastic-metal hybrid components. The microstructuredsurface enables the plastic to fill in undercuts and cavities in the molten state and thus to form an improved adhesive strength through microform closure. If the adhesive strength is essentially based on a materi al-locking connection, a blasted surface can achieve considerable increases in the strength of the plastic-metal connection. Force-fit and positive connections, on the other hand, benefit less from a blasted surface of the metal.Investigations into the influence of the joining geometry on the bond strength showed that geometries with pronounced joining characteristics achieve the greatest bond strength. It could be shown that of all geometric features, the increase of the undercut surface in the pull-out direction has the greatest influence on the bond strength.A further aim of this work is to investigate the tightness of the hybrid components. A test specimen close to the component was developed for this purpose. The leakage tests were then carried out on dry as molded and conditioned components under series test conditions. The adhesion promoter systems, which were disappointing in terms of bond strength, were not convincing in this test criterion either.Another approach to tigh ten the test specimen, based on the modification of the joining geometry, also had to be accepted as impracticable. The expectations that the shrinkage of the plastic resulting from the injection molding process could be used to improve the tightness by a skillful choice of the joining geometry were not fulfilled.The use of additional sealing elements, which are inserted into the mold together with the aluminum part and encapsulated by the plastic, finally turned out to be the right way.The features of a plastic-metal hybrid connection investigated in this paper were able to meet the expectations for use in transmission housings. This could either be achieved with already proven means, such as a shot peened surface, or after research work, such as the insertion of an additional sealing element.